The Computational Materials Processing (MatPro) department develops mathematical models for industrial production and processing of materials
The Computational Materials Processing (Matpro) department leads the way in cutting-edge research and development on industrial material processes, reactors, and components, utilizing advanced mathematical modeling and numerical methods. Our focus lies on the mathematical modelling of the underlying physical and natural phenomena using numerical methods, especially the Finite Element Method.
With over 30 years of experience in developing our own mathematical source code, our tools have been utilized in research projects with national and international industries, making our expertise highly sought-after worldwide. The Finite Element Method has enabled us to tailor-make our code for various materials and processes. Efficiently coupling microstructural models with macroscopic finite element methods is a key strength of our competence.
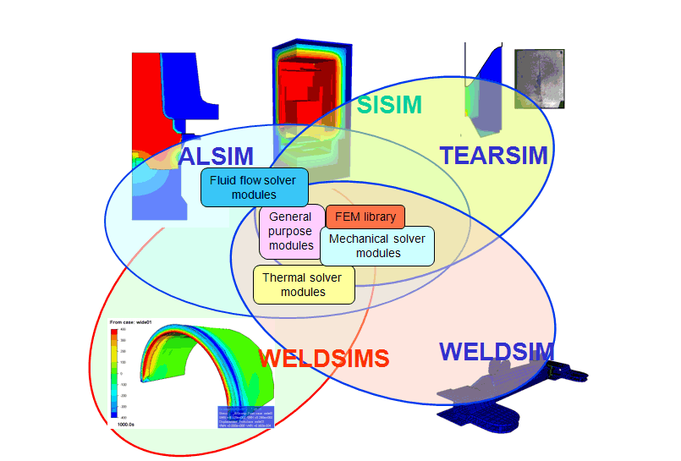
Our expertise primarily revolves around aluminum processes such as electrolysis, melt cleaning, continuous casting, and welding. We are proud to be running a DC-casting project with leading partners such as Alcoa, Aleris, Arconic, and Hydro. Our work has earned us international recognition, with partners from Germany, Poland, USA, and Canada.
We work closely with Norwegian and international industries to improve their production processes and products. Our research involves the development of mathematical models for a wide range of industrial material processes, including welding and additive manufacturing, production of hollow sheets and profiles by extrusion, shape casting, direct-chill casting, crystallization, and reactors for silicon production and CO2-capturing. We model a broad range of materials such as aluminum alloys, steels, silicon, titanium, and polymers, and the list continues to grow.
Our software for processing materials provides important input for evaluating performance and lifetime of products. We also engage in numerical analysis of floating, building integrated and rack mounted solar panels, and the electrochemistry of batteries. At Matpro, we strive to create a better future through research, and our projects contribute to the UN’s sustainability goals 7, 8, 9, 12, and 13.
Our workdays involve hands-on numerical modelling and development of our various in-house finite element software tools. We also use commercial and open-source modelling frameworks. Our researchers are constantly learning and building strong competence in both mathematics and the application domains, enabling us to solve specific challenges for industry customers through numerical studies.
Research Areas
Continuous casting of aluminium
Highly efficient and cost-effective process for production of semi-finished aluminum products such as billets, slabs, and ingots. At Matpro, we develop tools to optimize this process.
Shape casting with aluminium alloys and bronze
Manufacturing process for producing components with intricate geometries utilizing a permanent mold or a sand mold. At Matpro, we leverage our numerical modeling solutions to optimize the manufacturing process and product quality.
Welding of steels and aluminium
Critical process for the manufacturing of various products. At Matpro, we conduct research and provide numerical modeling solutions for welding processes, including arc, laser, and friction stir welding.
Additive manufacturing
Revolutionary process for producing high-quality, customized components with minimal material waste. At Matpro, we conduct research and provide numerical modeling solutions for various additive manufacturing processes.
Crystallization of silicon with the Czochralski method
we specialize in developing mathematical models for the crystallization of silicon using the Czochralski method. Our research focuses on optimizing the process and improving product quality, with the goal of helping industries to apply these models to their production processes.
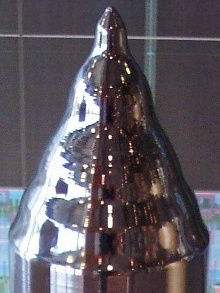
Aluminium electrolysis
Critical process in the production of aluminum. At Matpro, we conduct research on this process to model physical phenomena involved, optimize energy consumption, and reduce environmental impact, all while working closely with the industry to improve efficiency and sustainability.

Extrusion of structured sheets and profiles
Extrusion is a manufacturing process for producing structured sheets and profiles. At Matpro, we conduct research on this process, utilizing numerical modeling to optimize product quality for industries.
Ongoing projects
ALSIM
Modelling of semi-continuous casting of aluminium.
Madam
Development and production of metal alloys for powder-based additive manufacturing
SUCCEED
Sustainable and cost-efficient manufacturing of new solar technology in Norway
PROSun
Performance and Reliability of Ocean Suns floating photovoltaic Technology
HydroSun
Developing competence for hydro- floating PV (FPV) hybrid power plants
Be-Smart
Innovative Building Envelope for Sustainable, Modular, Aesthetic, Reliable and efficient Construction.
FLEX4FACT
Industrial cluster flexibility platform for sustainable factories to reduce CO2 emissions and to enable the energy transition.
QuickProd
Quick and simple assembly in automotive production enabled by a new casting technology
FLOW
Analysis and prediction of floating PV power plant performance
IMPRESS
Improved yield, lifetime and LCOE of floating solar power plants
MariSol
Develop and document knowledge related to the performance, reliability and degradation of integrated float and PV panel.
SolTak
Building-integrated solar cells for Norwegian roofs
Key Figures
EU/NRC Projects
Funding (NOK)