Well Flow Loop
The test facility contributes with high quality experimental data used:
- To improve and test basic multiphase flow models for prediction of pressure drop, holdup and flow regimes in multiphase flow, typically implemented in the OLGA simulator tool.
- For testing of instruments and components
Well Flow Loop at IFE in the Horizon JIP – Videos of wavy flow (YouTube link)
Description
The Well flow loop is designed for multiphase flow research in pipes with inclination ranging from horizontal to vertical, both upward and downward directed. The loop design and performance make this loop a valuable and unique tool for studies of flow phenomena that occur in typical well flow conditions as well as in transport pipelines. The loop is operated with a suitable model oil and water as the liquid phases and the dense gas sulphur hexa-fluoride as the gas phase. Maximum operating pressure for the loop is 8 bar. However, by utilising the dense gas we achieve gas densities that correspond to natural gas at a pressure as high as 65 bar.
The flow rig consists of a test section, a return section, a gas-liquid separator, an oil-water separator, pumps and compressors. Operational control of the loop is through a fully integrated computer system, which also handles the data acquisition. The oil flow rate is measured with Coriolis meters, the water flow rate with an electromagnetic meter and the gas flow rate by either vortex or turbine meters.
The test section is equipped with a 1 m long optical section made in acrylic. The optical
section allows for use of advanced photographic methods.
The loop was inaugurated in June 1994 and has provided valuable results for flow conditions typical for production from both oil and gas-condensate reservoirs. It has also been used with success in studies relating to flow induced corrosion. It is continuously being upgraded, particularly the scientific instrumentation.
Instrumentation
The Well flow loop is equipped with the following instrumentation:
Gamma densitometers (FVWM) for measurement of phase fractions, 2 & 3 phases
- dP-transducers for pressure gradient measurements
- High Speed Video camera for flow visualisation
- Iso-kinetic probe for droplet fraction measurements
- X-ray CT for measurement of holdup, fluid distribution and interface structures
- Laser Doppler Anemometer and PIV for detailed velocity & turbulence measurements
- Hot Film for measurement of wall shear stress
The X-ray CT systems have been designed in house over the course of a decade and are based on the use of two energy levels (aka Bi-Chromatic), which are required to distinguish three phases in the pipe flow. In total the laboratory has 10 detectors available in different configurations.
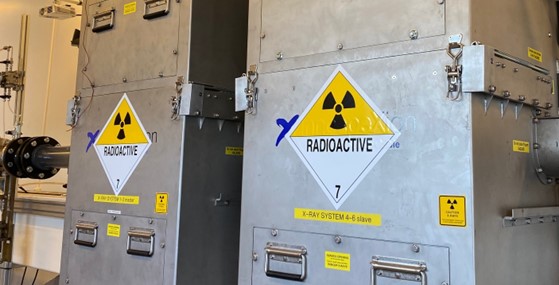
The picture shows the X-ray Computer Tomography system.
Technical specifications
- Loop material: AISI 316
- Fluids: Water, oil and gas
- Pressure: Max. 10 bara
- Test section dimension: ID 100 mm, length 25 m
- Test section material: Steel transp. PVC
- Variable inclination: 0-90 °C
- Gas phase: The dense gas SF6
- Superficial gas velocity range: 0.5 – 10 m/s
- Superficial oil velocity range: 0 – 2 m/s
- Superficial water velocity range: 0 – 2 m/s
Typical applications
Examples of flow phenomena that have been studied in the Well Flow Loop are:
- Droplet transport in the gas phase
- Oil-water-gas slug flow
- Roll-waves
- Local pressure gradients
- Long term liquid accumulation in gas-condensate pipelines
- Gas entrainment in liquid slugs and in the liquid layer in stratified flow