FALCON – IFE’s Flow Assurance Loop for CO2 transport.
The test facility contributes with research for safe and cost effective CO2 transport through experimental results used for modelling and validation of pipeline simulators.
The CO2 flow loop is a semi-outdoor test rig designed and built to accommodate test campaigns related to pipeline transport and well injection of pure CO2 or CO2 mixtures. The design and the instrumentation of the test facility serves the main motivation for building the flow loop, emphasizing pipeline flow of CO2 with phase transitions.
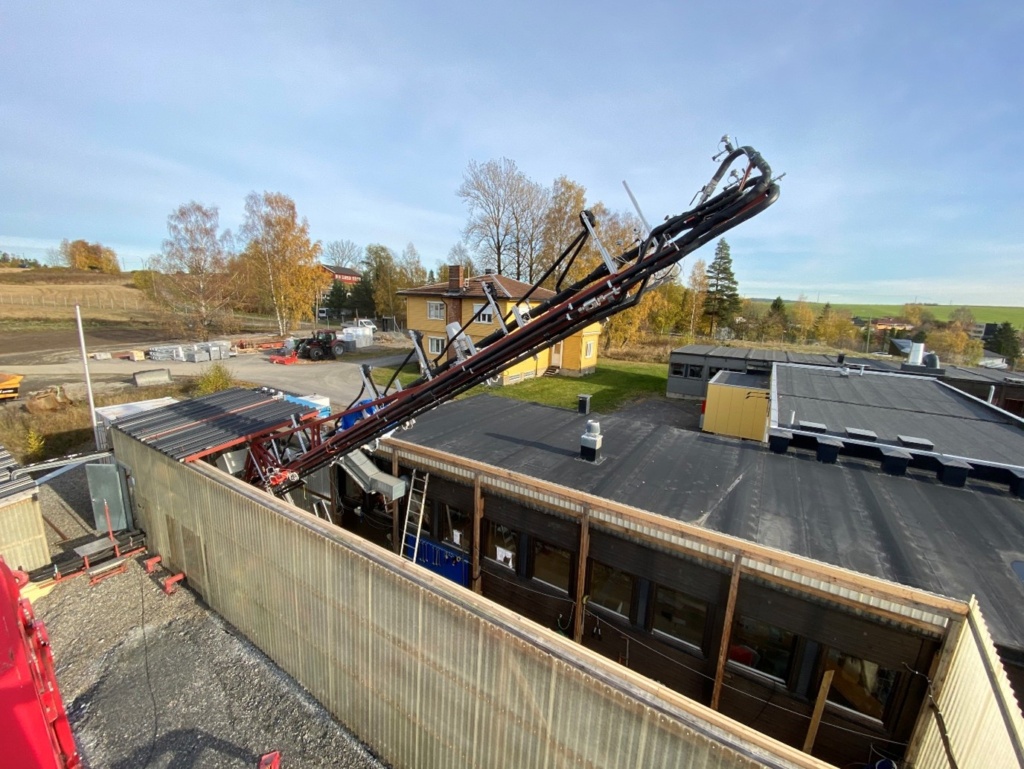
FALCON CO2 flow loop with an inclined test section. The inclination angle can be changed from full horizontal to full vertical
The FALCON test facility has a typical multiphase flow, closed loop design, as illustrated in below (Figure 2). It consists of a test section (5), a return section, a main separator (1), a liquid pump (2), a gas booster (3) and various auxiliary components. It also has a unique system for pressurization, consisting of a high-pressure cylinder (6) with a piston operated by a hydraulic aggregate.
For tests involving depressurization, flush-out and choking tests, for example, the loop is reconfigured as a once-through setup, normally using the storage tank (7) as a low-pressure reservoir/sink and the high-pressure cylinder with moveable piston as a mass flow source.
The flow rig has an advanced, combined heating and cooling system and is well insulated.
Operational control of the loop is through a fully integrated computer system, which also handles the data acquisition.
The test section can be inclined at any upward or downward inclination from horizontal to vertical.
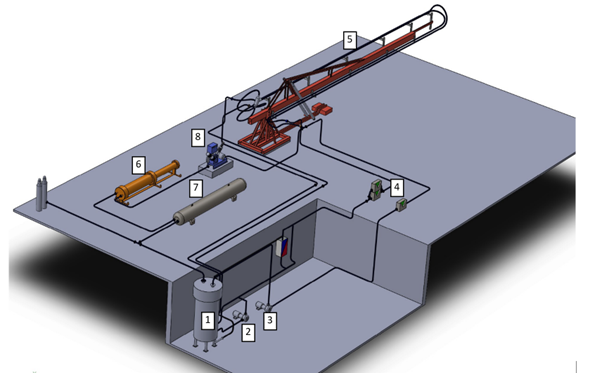
Schematic of the FALCON test facility with the key components. 1: Main separator, 0.5 m3, 2: Liquid pump, 3: Gas booster, 4: Flow meters, 5: Test section (ID = 44 mm), 6: High-pressure cylinder with piston, 0.08 m3, 7: Storage tank, 1.2 m3, 8: Compressor.
Topics that can be studied include:
• Basic steady state multiphase flow of CO2, measuring pressure drop, holdup and flow regimes in pipelines with inclinations form horizontal to vertical
• Flow through wellhead chokes with significant pressure drop, Joule-Thomson cooling and phase transition
• Various shut-in and startup scenarios with heat transfer and phase transition
• Pipeline and vessel depressurization for pipeline integrity during maintenance operations and unintended pipeline rupture
• Pressure transients caused by sudden valve closing; fluid hammering
The test facility can also be used for testing instruments and components.
Instrumentation
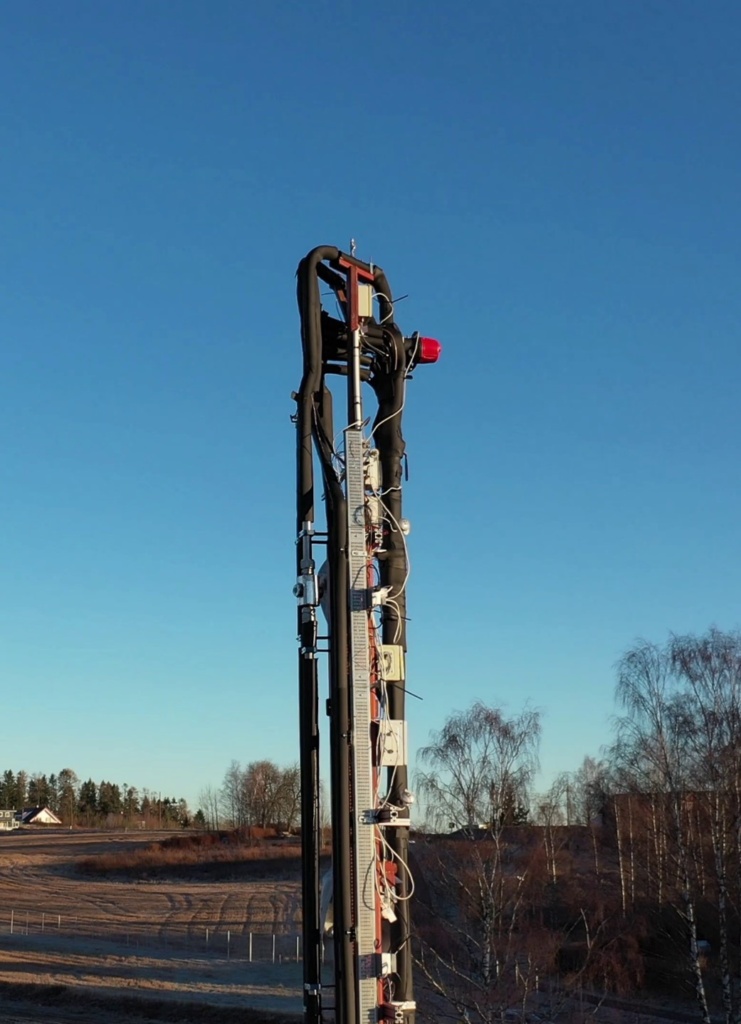
FALCON CO2 flow loop with the test section in vertical position.
The test facility is currently equipped with instruments for control of input parameters (flow rates, pressure and temperature) and for characterization of the flow and other phenomena in the test section. In addition to the many pressure and temperature sensors, these include:
• Flow rate meters (Coriolis and ultrasonic meters)
• Density meters
• Differential pressure transducers for pressure drop measurements
• Fast response pressure sensors
• Accelerometer and Acoustic Emission sensor for cavitation/vibration monitoring
• Two broad beam gamma-densitometers for phase fraction/holdup measurements
• A single-camera x-ray system for phase distribution mapping
• View cells and high-speed cameras
• An on-line system for sampling and analysis of CO2 streams from the loop for mole fraction of impurities and their partitioning between gas and liquid phases; Gas chromatography and infrared laser spectrometer for N2, CH4, H2O and O2.
Technical specifications
Loop material: AISI 316
Fluids : Pure CO2 and CO w/impurities, e.g.N2, CH4, H2O, O2
Pressure: Max. 150 bara
Temperature range: -150 °C to +50 °C
Test section: ID 44 mm, Length = 13 m
All pipe inclination, from -90° to + 90 °
Superficial vapour velocity range: 0 – 10 m/s (55 Am3/h)
Superficial liquid velocity range: 0 – 3 m/s (15 Am3/h)
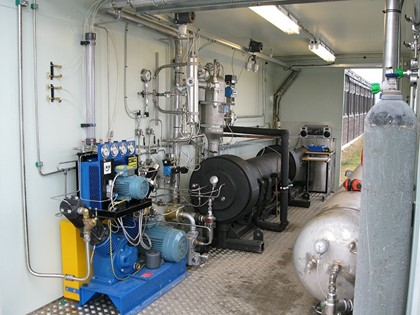
Equipment for pressurization and pressure control of the test rig
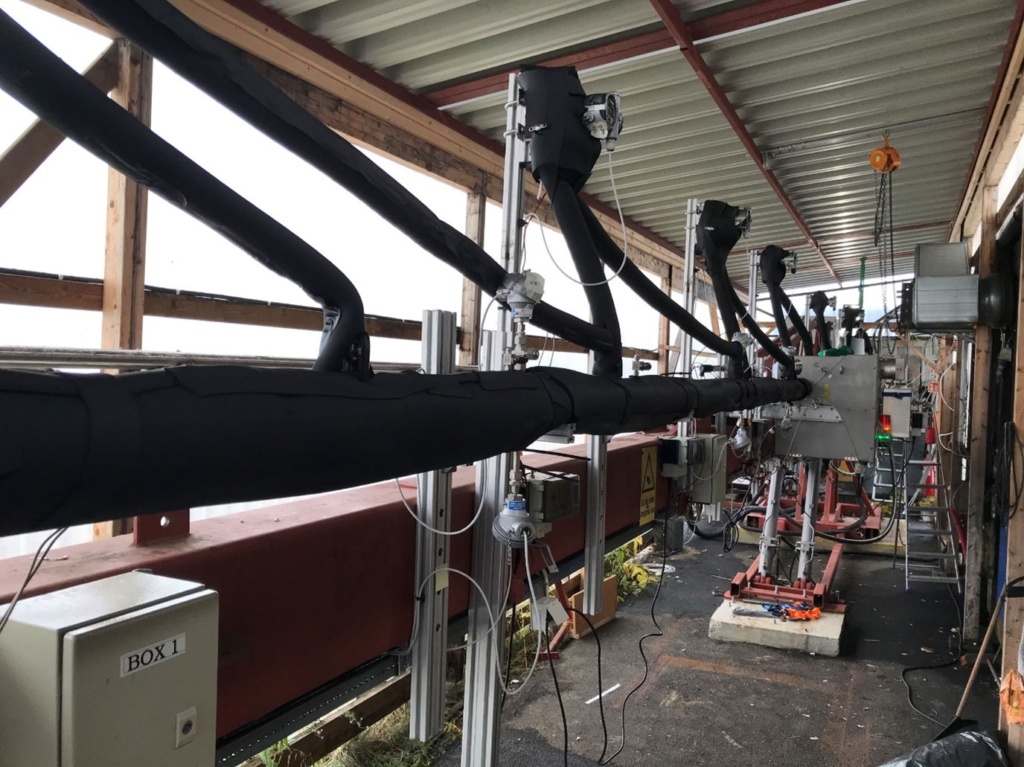
Test section in horizontal position.
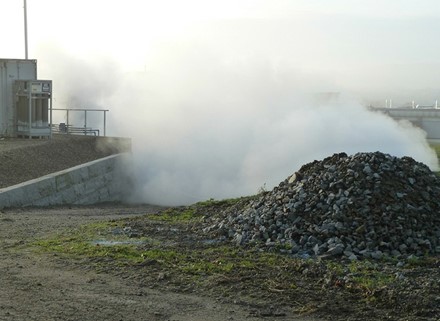
FALCON CO2 flow loop, field test on the dispersion of CO2 from a simulated pipe rupture